How to Become a Shipper of Choice
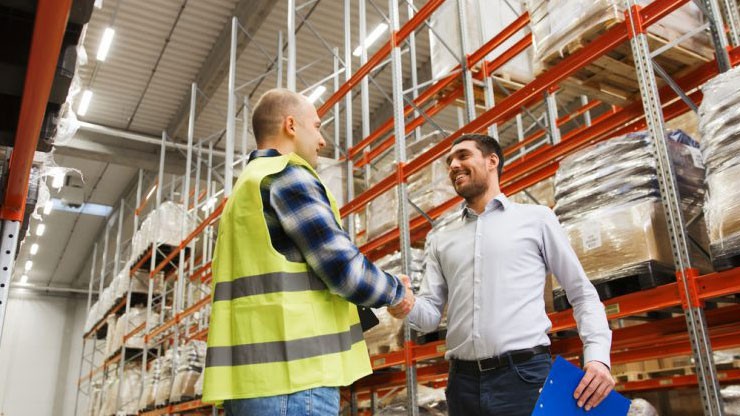
When it comes to on-time delivery and a positive shipper-carrier interaction, every player in the supply chain has a part. Manufacturers and shippers must ensure the product is ready to go for pickup, drivers require optimal and agile routing, and receivers must have the correct equipment to unload the product. As businesses know, the supply chain is much more complicated; careful planning and consistent communication can help ensure the process from pickup through delivery goes as smoothly as possible. Read on to learn some of the most important considerations shippers and receivers should keep in mind to help freight end up in the right place at the right time.
Appointment Scheduling
Is your facility first-come, first-served (FCFS) or do you hold strict appointment times?
Due to the unpredictable nature of transportation services, it’s important to remain as flexible as possible. Delays happen, and everybody must work together to respond when timelines tighten. Ensure your business has protocols in place to communicate and organize appointments.
Are facility hours posted clearly and is there an after-hours delivery plan in place?
Many shipments require a driver to speak with the shipper or receiver when loading or unloading. If the facility is closed when a driver arrives, contact information or a contingency plan must be communicated in order to avoid a costly disruption for the shipper or receiver.
Is there an appointment rescheduling process in place?
Appointments do occasionally need to be rescheduled due to a variety of reasons. Ensure your company provides a plan to drivers and freight brokers when adjustments are made.
Unloading Process
Are your docks easily accessible?
Depending on the volume of shipments that come through your location, you may need to consider utilizing more than one dock if you have enough staff. All open doors should have a crew available to help unload. In addition, hand unloading may be necessary for some shipments and must be accounted for in staffing.
Is your facility well-staffed, well-equipped, and ready to unload when necessary?
Unloading freight can take a lot of time – especially in situations where a hand-unload is necessary, such as non-palletized or sensitive freight. Along the same lines, a single person using a forklift to unload palletized cargo can also take a fair amount of time. Organizing unloading crews and maintaining adequate staff keeps your facility efficient.
Do drivers know where to go to unload as they arrive at the facility?
Signage and the ability to contact a member of the team at the shipping or receiving facility will ensure drivers are able to access their dock or loading/unloading zone as quickly as possible. Precious time could be wasted if direction is unclear.
Does the shipping/receiving location have necessary equipment available to load/unload?
Pickup and delivery run smoothly when everything is in place, including equipment such as lift gates, pallet jacks, forklifts, and so on. Understanding the needs of each shipment and preparing for pickup or delivery is imperative to keeping products moving throughout the supply chain.
Facilities
Does the facility have a place where the driver can shut down overnight or during hours of service (HOS) restrictions?
Due to Federal Motor Carrier Safety Administration (FMCSA) regulations, drivers must follow strict HOS rules. Before shutting down, truckers must find a safe and legal place to park. Facilities that provide such accommodations are a big help for drivers. If you do not have a safe, legal location for drivers to spend time off the road, provide a list of nearby locations that allow trucks to park for food, sleep and rest time.
Do drivers have a place to wait or use the restroom if necessary?
Adjustments to schedules will happen. Another way to ensure freight gets moving as quickly as possible is to ensure drivers have facilities available while they wait, including a restroom and even vending machines. Schedule changes can be recouped if the driver is able to avoid additional stops after visiting the pickup/delivery location.
Is there a plan in place for appointments that are rescheduled for the next day?
When the pickup or delivery of a shipment is delayed overnight, a driver needs to find a place to sleep. Depending on timing restrictions, it may be necessary to have the driver as close to the facility as possible in order to get the freight moving through the supply chain. Consider allowing drivers to park and wait or sleep at the shipping/receiving facility for situations when delays happen but timing remains tight.
Here’s the bottom line:
Transportation services can be inherently unpredictable. A chain of events could stall the progress of a shipment from pickup to delivery. These disruptions can create extra costs, delayed deliveries, and unhappy customers. When the needs for all components of the supply chain are considered throughout the shipping process, it can be much easier to catch up when things fall behind. Check out our post about Creating Driver-friendly Shipping and Receiving Facilities.